Worker Safety and compliance Monitoring System for a manufacturing unit
Project Overview
A leading machine parts manufacturing company wanted to ensure worker safety within its factory floor, warehouse and other restricted zones. While manual safety protocols turned out to be error prone and non-spontaneous, the client wanted to develop an automated system capable of real-time monitoring safety protocols, worker tracking and predicting potential emergencies or hazardous situations. The goal was to create a seamless process that would enhance safety compliance while reducing the need for manual supervision.
Growth Tracking
100%
Compliance of safety equipment protocols
100%
Hours of training in first 3 months only
95%
Reduction in cases of workplace accidents
Major Challenges
Manually supervising safety protocols and ensuring compliance across a large manufacturing facility was a challenging task for the company.
The absence of an automated system resulted in inefficiencies and increased the risk of accidents or non-compliance with safety regulations.
There was a clear need for an automated solution to streamline safety processes and improve overall compliance.
Solution
The company deployed the "iotasol Machine Vision System" to process data from cameras installed throughout its factories. This system integrated seamlessly with sensor data, allowing for comprehensive monitoring of safety protocols like distraction detection, high risk area supervision, restricted areas monitoring and employee health status tracking in real-time.
The system generated alerts and valuable insights, leveraging machine learning algorithms to predict potential hazards or emergencies. These insights were then used to prompt manual verification, take necessary actions, and continuously improve the overall safety system.
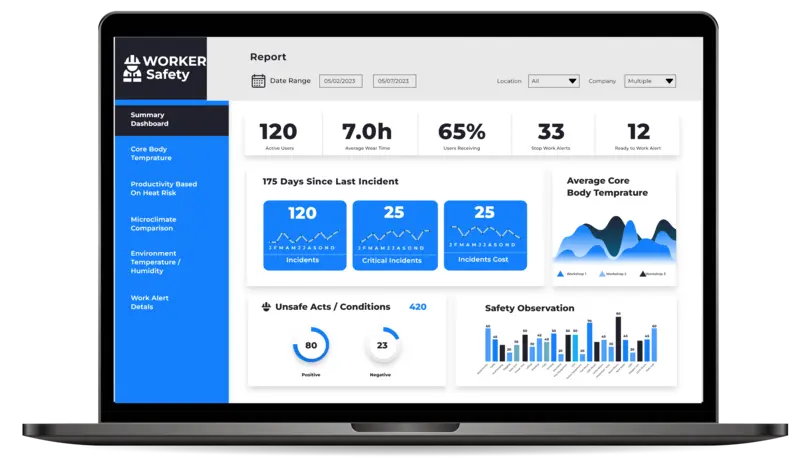
By implementing this comprehensive solution, the manufacturing company successfully addressed its safety challenges, ensuring a safer working environment for its employees while enhancing operational efficiency and compliance with safety regulations.
Outcome
-
The implementation of the automated safety monitoring and prediction system brought significant benefits to the manufacturing company.
-
Supervising and managing worker safety became significantly easier and more efficient.
-
As a result, the accident rate within the facility decreased, and workers reported feeling safer while operating in high-risk areas.
-
The company achieved a higher level of safety compliance and reduced the risk of costly accidents and disruptions to operations.
Client Stories
Get in Touch for a live demo of IoT solutions over a workshop
Hear it From Our Clients
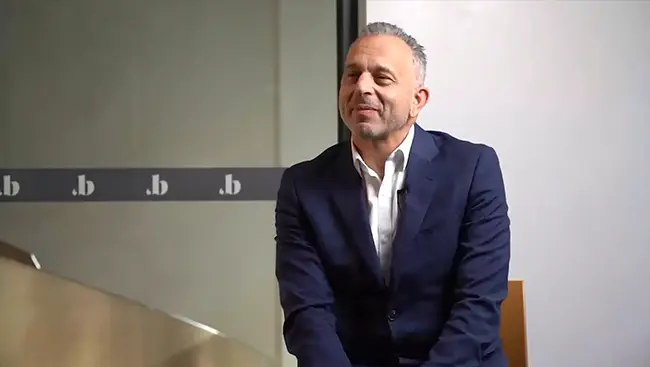
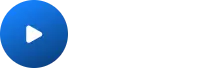
Taxtalk is a digital platform that provides premium tax accounting services to people and businesses across Australia. Hear Dominic Barba , CEO, Taxtalk speak about how iotasol helped them switch from a traditional business model to a technologically advanced and sustainable model
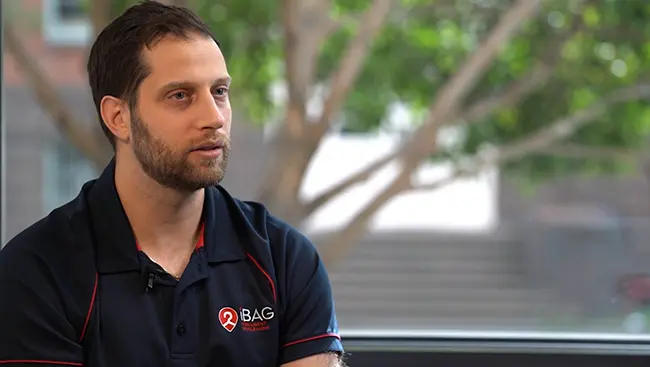
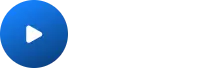
iBAG is an intelligent dry cleaning app that automates operations for service providers and simplifies customer experience. Aaron Pino, CEO of iBAG shares how iotasol, as their tech partner, crafted a versatile, futuristic app. He values iotasol's unwavering support and dedication
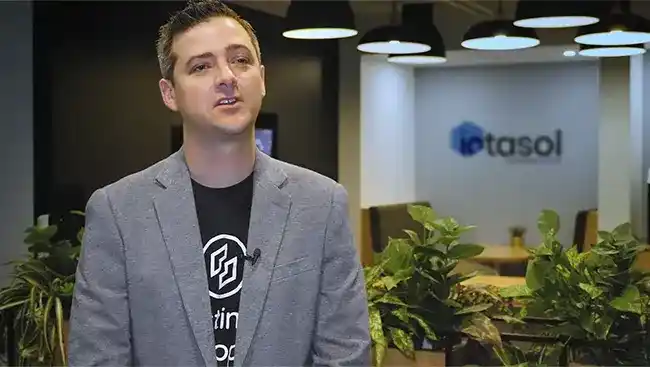
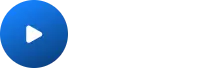
Listing Loop is a digital platform that allows early access to exclusive off-market properties across Australia. Hear it directly from the CEO of Listing Loop on what influenced his decision to entrust iotasol with all development work following some initial testing and how our work brought a significant impact on key business matrices
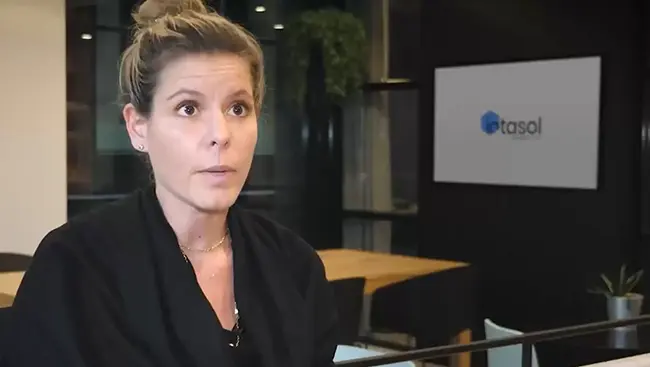
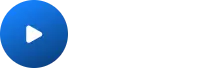
Carers Couch, connecting cancer caregivers with vital support, hails iotasol for their pivotal role. Martina Clark commends iotasol's trustworthiness and commitment, she says that iotasol goes beyond the role of a tech partner to ensure the vision behind a product is lived upto