Factory operations today are facing mounting pressures, from rising labor costs and inefficiencies to the challenge of meeting regulatory compliance standards. Amid these growing challenges, Artificial Intelligence (AI) is emerging as a game-changer for manufacturers striving to stay competitive.
The role of AI in factory automation is becoming more important than ever. It’s changing the way manufacturing works by helping factories run more efficiently, produce better-quality products, and reducing costs. In this blog, we’ll walk you through how AI is making a big difference in factory operations. From spotting quality issues with smart cameras to predicting equipment problems before they happen, AI is helping factories work smarter, not harder.
We’ll also share real-world examples and success stories that show just how impactful AI can be. By using AI, manufacturers can tackle challenges, meet industry regulations, and set themselves up for long-term success. Let’s dive in!
The Evolution of Factory Automation with AI
Factory automation has come a long way since the days of manual assembly lines and basic machinery. The introduction of automation technologies in the 20th century brought major changes to the manufacturing landscape. However, the real shift began with Industry 4.0, which focused on integrating AI-driven innovations to enhance factory operations.
In the traditional assembly line, machines performed repetitive tasks, but they lacked the intelligence to make decisions autonomously. Today, smart factories powered by AI use advanced technologies like machine learning, AI-driven manufacturing solutions, and smart factory technologies to mimic human decision-making, adapt to changes, and optimize processes in real time.
For example, in a modern AI-powered factory, machines not only carry out tasks but also communicate with each other and the central system to adjust production processes automatically.
This evolution marks a significant step forward in creating factories that can learn from data, adapt to changing conditions, and operate efficiently with minimal human intervention.
Key Applications of AI in Factory Automation
AI for Quality Control
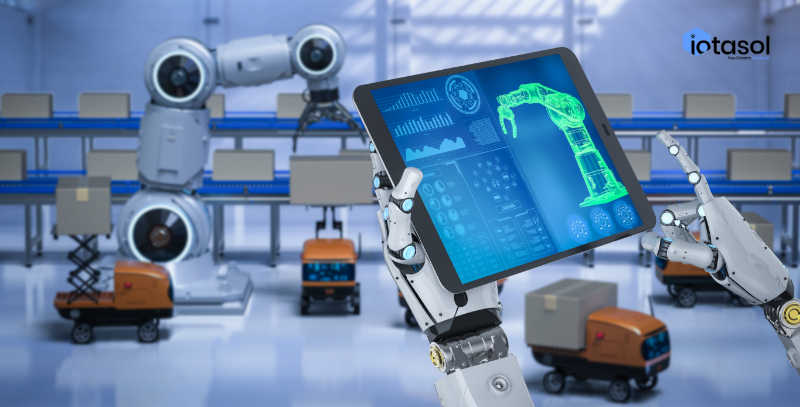
Quality control is a critical area where AI has made a significant impact in manufacturing. Machine vision systems, integrated with AI, can analyze real-time production data to detect defects and quality issues with a precision that far exceeds human capabilities. AI algorithms can instantly compare product images to a set of predefined quality parameters and flag any discrepancies.
For example, in the food production industry, a company used machine vision powered by AI to monitor the appearance of packaged products on the assembly line. The result? A 30% reduction in defective products reaching the market. AI can also reduce the need for manual inspections, speeding up processes and improving overall product quality.
Predictive Maintenance
Another critical application of AI in factory automation is predictive maintenance. AI-powered systems analyze sensor data from machines and equipment to predict when a part is likely to fail, allowing plant managers to perform maintenance before a breakdown occurs. This helps prevent unplanned downtime and extend the lifespan of costly equipment.
In pharmaceutical plants, for instance, AI can analyze vibration, temperature, and pressure data from motors and other machinery to anticipate motor wear or potential failure. By addressing these issues before they result in operational downtime, manufacturers can significantly reduce maintenance costs and ensure smoother production flows.
Production Optimization
AI for production optimization focuses on making real-time adjustments to workflows and reducing bottlenecks. Much like a GPS system in a car, AI analyzes data from different parts of the production process to find the most efficient route forward. If a bottleneck is detected, AI can adjust the workflow to alleviate pressure on that point, improving throughput and minimizing delays.
In smart manufacturing systems, these real-time optimizations contribute directly to more efficient operations and greater overall productivity.
Supply Chain Management
AI is also transforming supply chain management by improving demand forecasting and inventory management. AI models analyze historical data, weather patterns, and market trends to predict future demand, helping manufacturers optimize their supply chains. For example, a beverage company used AI to predict seasonal demand fluctuations and adjust inventory levels accordingly, preventing shortages and overstocking.
This predictive capability not only reduces costs but also ensures that production lines are never idled due to supply chain disruptions.
Benefits of AI in Industrial Automation
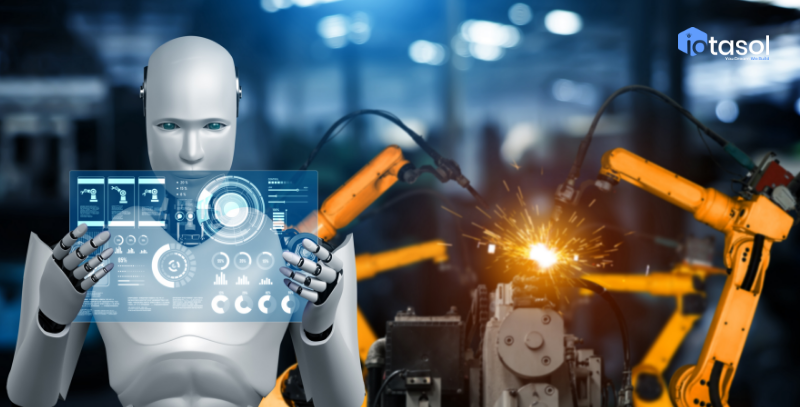
AI offers several critical advantages to manufacturers seeking to improve operational efficiency and reduce costs. Here are some of the most significant benefits:
-
Efficiency Gains: AI enables faster production cycles by automating complex tasks. This reduces human error and accelerates operations. For example, AI-driven robots can handle routine tasks like assembly, packing, and labeling, freeing up human workers for more value-added tasks.
-
Cost Reduction: By implementing AI for predictive maintenance and quality control, manufacturers can avoid costly repairs and minimize waste. The ability to predict equipment failures before they happen can also reduce the costs associated with unplanned downtime.
-
Compliance and Sustainability: AI helps manufacturers maintain compliance with industry standards and regulations. In the pharmaceutical sector, AI-driven reporting systems ensure that manufacturers are consistently meeting regulatory requirements, reducing the risk of fines or product recalls.
-
AI also contributes to sustainability by optimizing energy consumption and minimizing waste. For example, AI can adjust production speeds or processes to optimize energy use, helping manufacturers achieve both environmental goals and cost savings.
Real-World Success Stories
The practical applications of AI in factory automation are vast and impactful. Here is a story of how iotasol’s AI-driven solutions helped transform a key client’s manufacturing operations:
Pharmaceutical Industry
One of our clients, a leading pharmaceutical company, faced packaging defects that led to costly recalls and compliance risks. iotasol implemented an AI-powered machine vision system, leveraging high-resolution imaging and machine learning algorithms. This solution detected packaging defects with unmatched accuracy, reducing waste and enhancing compliance. As a result, the company saw a 90% reduction in RMAs and improved customer satisfaction while maintaining regulatory standards.
This case demonstrates how AI-driven solutions can drastically improve manufacturing efficiency, reduce waste, and ensure compliance in highly regulated industries.
The Role of AI and IoT in Smart Factories
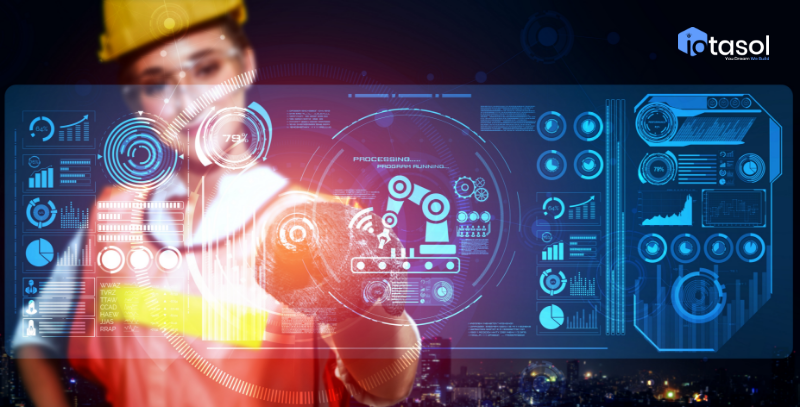
AI and the Internet of Things (IoT) are revolutionizing factory automation by creating interconnected systems that collect and analyze data to drive decision-making. AI and IoT in factories enable manufacturers to track performance in real time and make adjustments quickly, ensuring optimal operations.
In a smart food processing factory, IoT sensors monitor critical variables like temperature and humidity. When deviations from optimal levels are detected, AI adjusts the production process accordingly, preventing spoilage and ensuring the quality of the final product.
This synergy between AI and IoT creates a factory environment that is more responsive, efficient, and self-optimizing, paving the way for the next generation of smart factories.
Challenges in AI Integration
While AI brings tremendous benefits to factory automation, its integration comes with challenges that manufacturers must address:
-
Implementation Costs: Deploying AI solutions requires upfront investment in hardware, software, and training. However, the long-term savings from increased efficiency and reduced maintenance costs often outweigh the initial costs.
-
Workforce Retraining and Upskilling: AI implementation necessitates a shift in the workforce. Employees must be trained to work alongside AI systems and develop new skills to manage and troubleshoot them.
-
Ethical and Security Concerns: AI systems must be secure from cyber threats, and ethical considerations regarding data privacy and decision-making transparency must be taken into account.
Think of integrating AI into a factory as solving a complex puzzle. Each piece, whether it’s training, security, or system compatibility, must fit together to achieve success.
Future Trends in AI and Automation
The future of AI in factory automation is bright, with exciting innovations on the horizon. In Industry 4.0, AI is expected to drive further automation, particularly with the rise of generative AI. This technology could revolutionize the design and development of new manufacturing solutions, from process optimizations to entirely new production models.
Generative AI could help engineers design more efficient systems, automate product design, or even predict new manufacturing methods, making factories more agile and adaptable to future demands.
As these technologies continue to evolve, we can expect even greater efficiencies, lower costs, and smarter factories that continuously optimize themselves.
Conclusion
AI is revolutionizing factory automation by streamlining processes, improving product quality, and reducing operational costs. From predictive maintenance to quality control and smart factory technologies, AI is transforming how manufacturers operate in the modern era. With its ability to adapt, optimize, and ensure compliance, AI is empowering manufacturers to stay ahead in an increasingly competitive landscape.
Ready to take the next step toward modernizing your factory? Contact iotasol for a free consultation and discover how our AI-driven solutions can optimize your manufacturing processes and drive sustainable growth.
FAQ
What is AI’s role in Industry 4.0?
AI plays a crucial role in Industry 4.0 by enabling factories to operate smarter, with greater efficiency and autonomy. Through AI, machines can learn from data, make decisions, and optimize production processes in real time.
How does AI improve quality control?
AI improves quality control by using machine vision systems to detect defects, ensuring consistent product quality. AI can instantly analyze production data and identify discrepancies that may go unnoticed by human inspectors.
What are the cost benefits of predictive maintenance?
Predictive maintenance helps avoid unexpected equipment failures, reducing costly downtime and maintenance expenses. By addressing issues before they occur, companies can save on repair costs and ensure smoother operations.
Are AI solutions scalable for small manufacturers?
Yes, AI solutions can be tailored to fit factories of all sizes. Scalable AI-driven manufacturing solutions allow small manufacturers to benefit from automation without the need for large capital investments.
How does AI ensure regulatory compliance?
AI can help ensure compliance by automatically tracking and reporting data in accordance with industry regulations, reducing the risk of human error and ensuring that all processes meet required standards.